US Duct
Products
Simple, fast, easy ductwork for your application
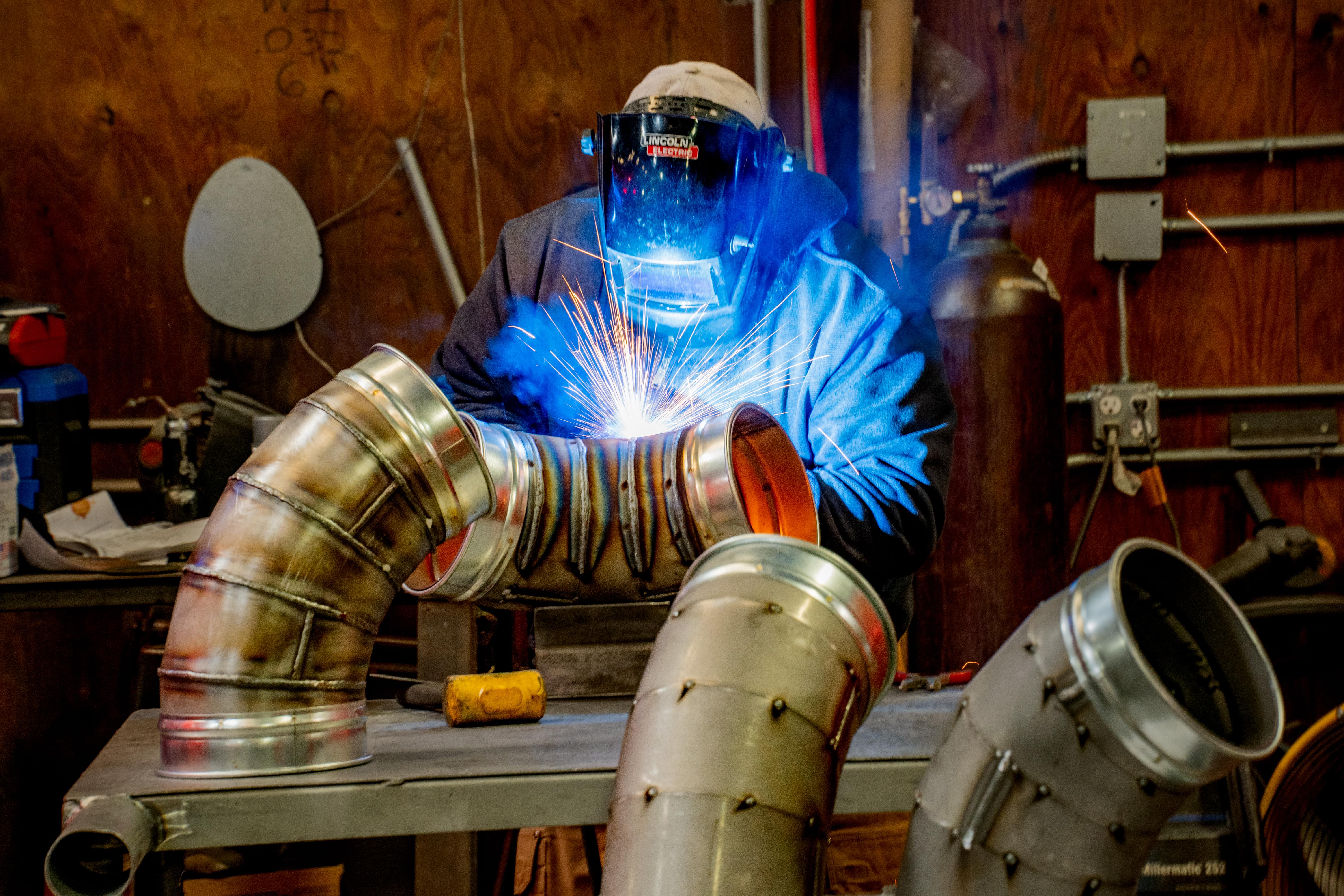
Filters
Clamp-Together Duct
DuctQuote
Legend Baghouse Collector
Legend HEPA Fume Extractor
Legend Hanging Fume Arm
Legend Industrial Rotary Airlock
Legend Inline Separator
Legend Quick-Change Hopper
Legend Self Dumping Hoppers
Legend Self-Cleaning Fume Extractor
Legend Standard Fume Extractor
Silencers
US Tubing
Angle Rings/Flanges
Automatic Butterfly Valve With Half Moon Stops -AC Voltage
Automatic Butterfly Valve With Half Moon Stops -DC Voltage
Automatic Cut-Off Gate
Automatic Diverter Valve
Automatic Gates (AC Voltage)
Automatic Gates (DC Voltage)
Ball Joints
Bell Mouths
Butterfly Valve
Cable Hangers
Connection Adapter
Explosion Isolation Valve
Fan Transitions
Flap Exhaust Valves (Flap Stacks)
Floor Sweeps
Hat Style Saddle Duct Hangers
Horizontal Oil Mist Accumulator
Hose Adapters
In-Cut Branches
Jet Caps
Legend Cyclone
Legend Spark Trap
Legend Standing Fume Arm
MRI Quench Vents
Machine Adapters
Manifolds
Manual Air Tight Blast Gate
Manual Butterfly Valve
Manual Cut Off Half Gate
Manual Diverter Valve
Manual Full Cut Off Gate
No Loss StackHead
Oil Mist Curbs
Rain Caps
Rolled Lip Duct Replacement Clamp
Roof Stanchion, 24"-48" wide
Roof Stanchion, 60" - 72" wide
Saddle Duct Hangers
Segmented Elbows
Single and Double Branches
Spark Trap
Special/Custom
Stitched Elbows
Swivel Joint
T-Branches
Teardrop Hangers
Thermoplastic Flex Hose
Tubed Elbows
Vertical Oil Mist Accumulator
Vibration Dampener
Y-Branches
No results found.
There are no results with this criteria. Try changing your search.
Talk to a Duct Guy or Gal
Get started on a solution tailored to your needs, or explore our range of inline separators, self-dumping hoppers, and baghouses for even more ways to optimize your workspace.